Waste heat is often generated in industry. The temperatures required by the process at Jackon’s Muurla plant are very high, but the high-temperature technology of Oilon’s industrial heat pumps can match these demands.
Jackon Group is the leading insulation manufacturer in the Nordic countries. At the end of last year, ThermiSol, Tupler, Epsira and Pohjoismainen Solumuovi were merged into Jackon Finland Oy, part of the Norwegian family-owned Jackon Group. The Group produces energy-efficient solutions for construction and industry, with a broad range of EPS, XPS and EPP insulators, packages and components.
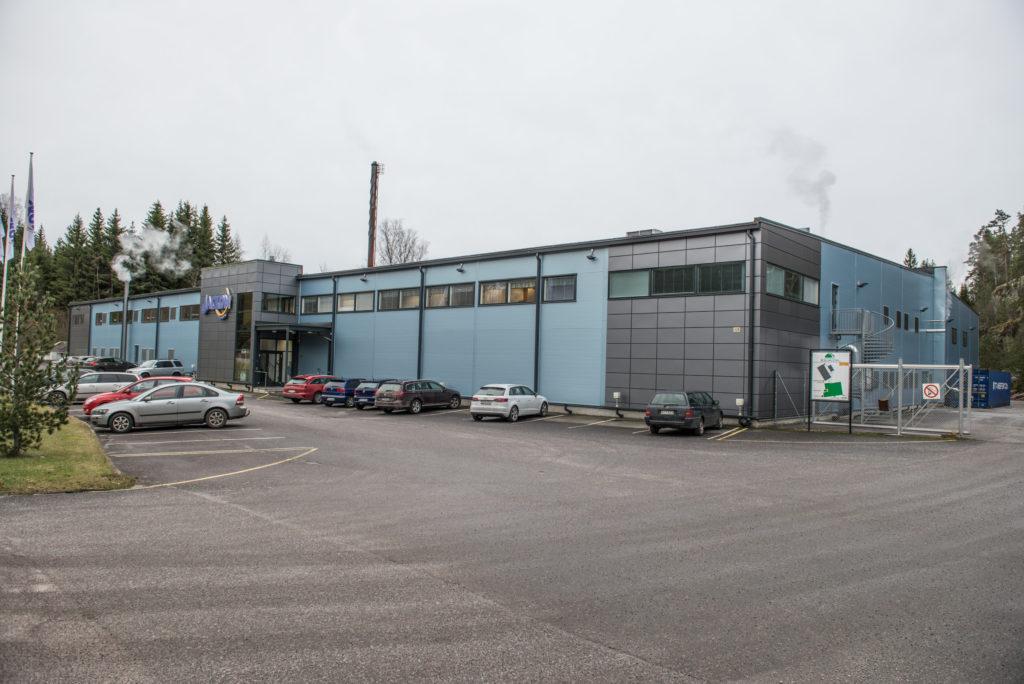
Energy efficiency has been studied for a long time
The Muurla plant was practically rebuilt in early 2009, following a devastating fire on Finnish Independence Day, December 6, 2008.
All the firm’s different expanded plastic foam products – with the exception of insulation boards – are made by expansion in a mould. Polystyrene (EPS), polyethylene (EPE) and, increasingly, polypropylene (EPP) are used as raw materials. The expansion, or sintering, takes place with saturated steam at a temperature of about 120°C for polystyrene and about 140°C for polypropylene.
The sintering takes place in 20 large “furnaces”. The expansion cycle takes just 1-2 minutes, after which the mould is cooled down to about 90°C. The process consumes a lot of energy. In addition heat is required in four heat treatment ovens in which EPE and EPP products are placed to stabilise after sintering. EPS does not need this post processing.
“Ten years ago, we started researching for more efficient use of energy,” says Jukka Mälkönen, production manager at the Muurla facility. “The cooling of the moulds produces 50-60°C water, which is traditionally cooled to 30-40°C in a cooling tower. It consumed 3,000 megawatt hours (MWh) of energy per year for small birds.”
“Even then we used the extra heat to the fullest extent, but for example, we were not able to produce the high temperature – almost 100°C – needed for the heat treatment ovens. Heat pumps at that time were not able to produce those temperatures.”
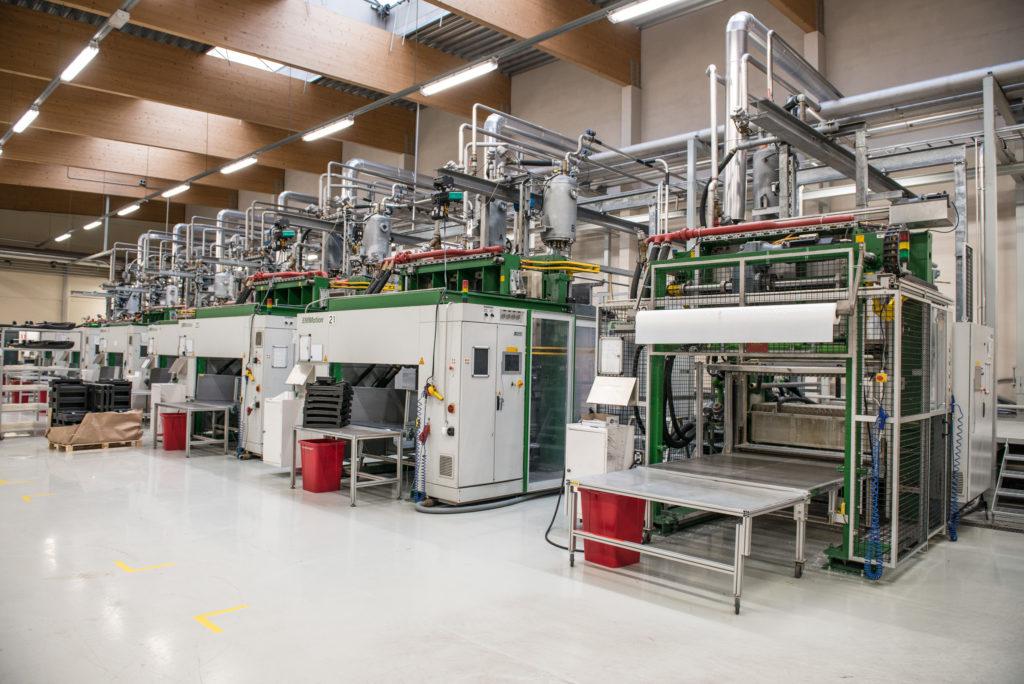
Planning required a lot of calculation skills
Some years later Mälkönen read an article according to which heat pumps had reached temperatures above 100°C. He contacted consultants in the field and met a few, but they were not offering Oilon’s technology. They offered complete solutions, but the prices of their proposals seemed very high.
“There was a lot of calculation in the system design, but we knew best because we knew the process exactly,” Mälkönen continues. “We previously had a strong relationship with Oilon because we used their burners, for example, in the steam boiler. We started to design the whole system with them, because they have long experience of high-temperature heat pumps and know-how to make the calculations.”
“We decided to make the necessary heat exchangers and assemble the system ourselves. Oilon helped us with the design and sizing of various details and provided the suitable heat pump for the purpose.”
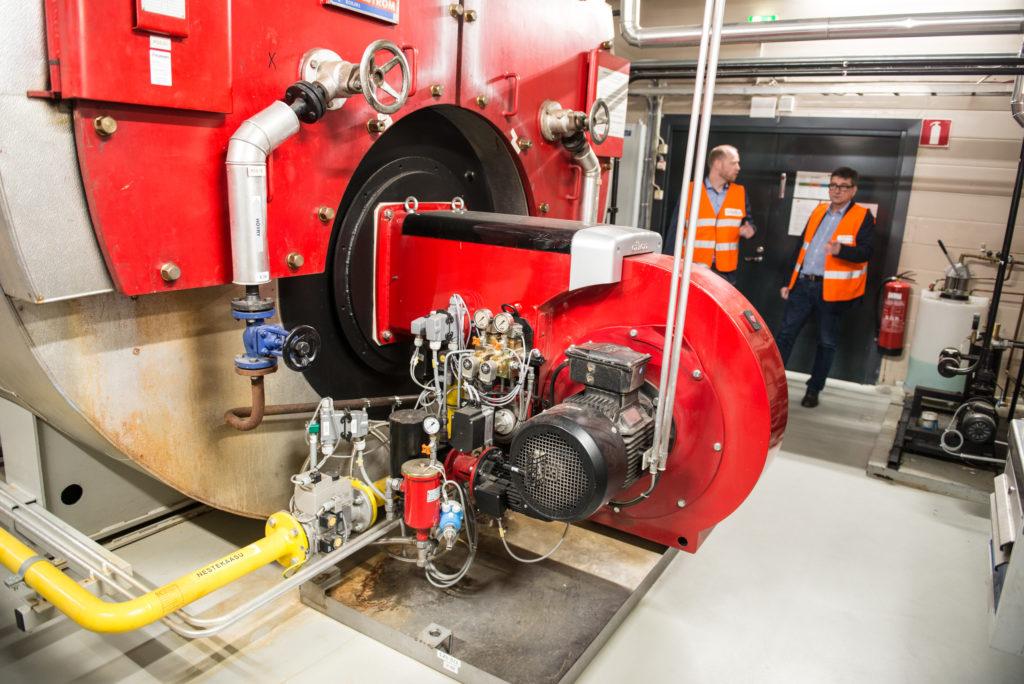
Several high-temperature heat streams
The cooling water from the moulds is fed into a 20m3 tank that has a temperature of around 50-60°C. The heat pump uses this cooling cycle as a source of heat, cooling the water to 40°C, while reducing the need to use cooling towers.
The heat pump produces about 95°C water, which is used to heat the after-treatment ovens and premises. This replaces the use of steam and electricity. On the other hand, the heat pump is also used for heating the boiler feed water.
Sintering steam is still produced at the factory in a liquefied petroleum gas (LPG) heated boiler. Steam boiler feed water comes from the municipal water mains with an inlet temperature of 6-7°C and is heated to about 60°C by direct heat recovery. The heat pump further heats the boiler feed water up to about 80°C.
High temperature – almost 100°C – is also needed in the impregnation of the raw material and more than enough energy is also available to heat the premises. All in all, the thermal energy available is more than required by the facility. Some of the heat goes to the cooling tower since, for example, the municipality is not interested in using it for district heating in Muurla village.
Lots of power with good efficiency
“We ended up with the Oilon ChillHeat P 150 heat pump,” says Martti Kukkola, Chief Business Officer, Industrial heat pumps and chillers at Oilon. “It is the right size for this system and it reaches very high temperatures. The two compressors of the heat pump are inverter controlled, providing excellent efficiency and a very wide capacity control range.”
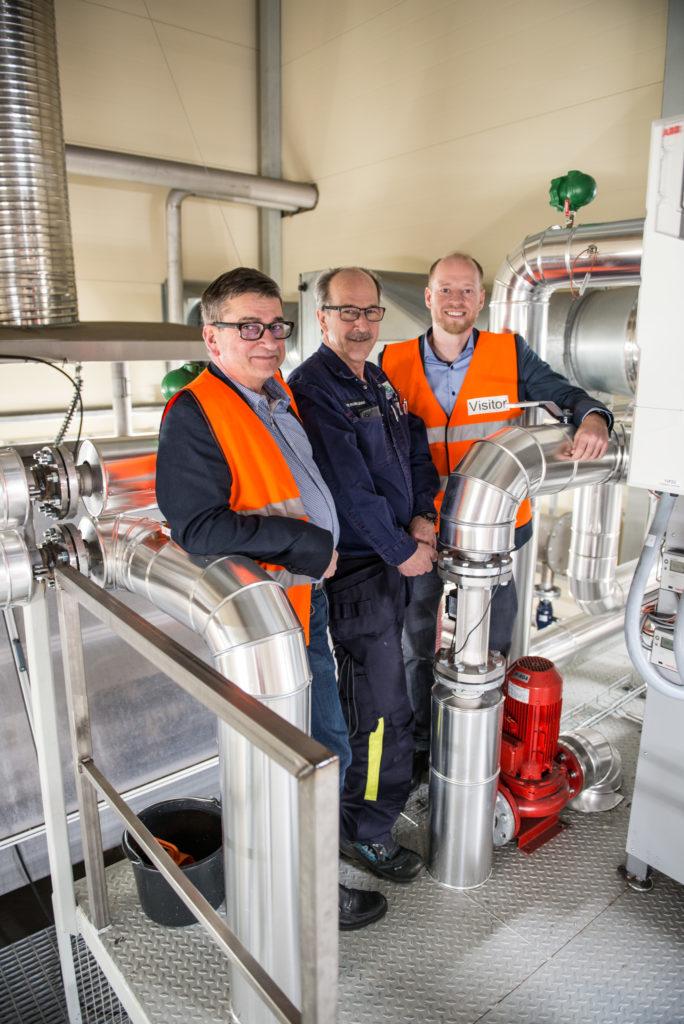
“Jackon has a lot of waste heat at 50-60°C. However, the required process temperatures are so high that it would not be possible to use the waste heat with a conventional heat pump. Conventional heat pumps have yields in the range of 50-60°C, which is only the starting point for the requirements here.”
Kukkola extensively praises the expertise of Mälkönen and his staff in, for example, demanding implementation of critical tube and shell heat exchangers. “The client built the system by themselves. They have a lot of expertise.”
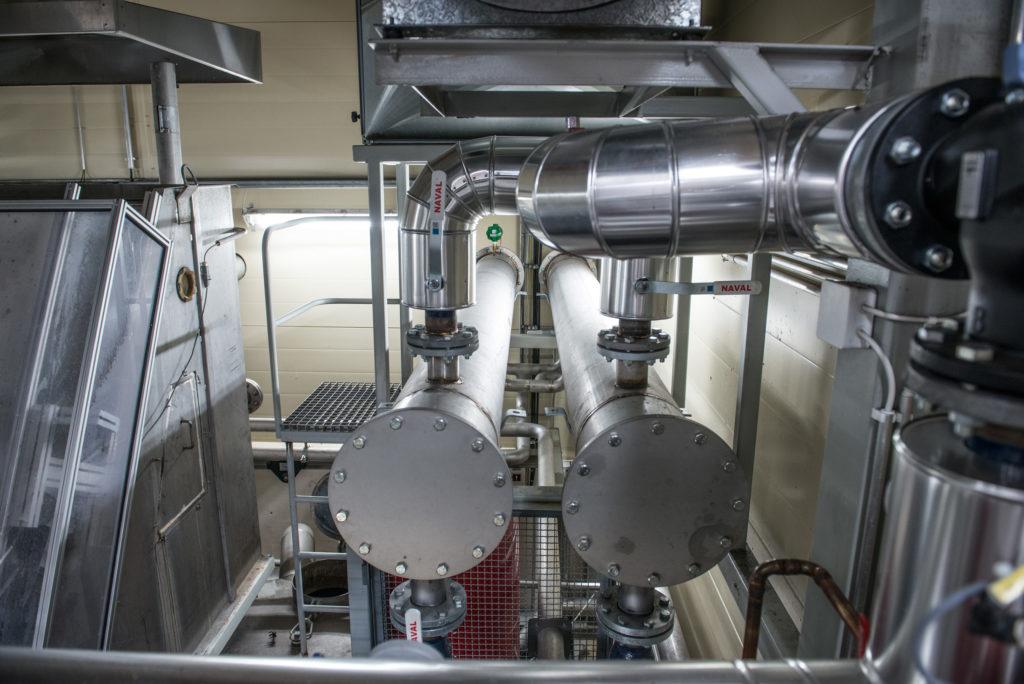
The ChillHeat P150 heat pump delivered to Jackon has a total rated heating power output of 372kW and a COP (coefficient of performance) of 3.2, despite producing almost 100°C water.
The heat pump refrigerant (or heat transfer medium) is R1234ze. It is a new generation refrigerant which, together with the P-Series heat pump, is capable of producing a temperature of 100°C. The substance has a very low global warming potential (GWP) of less than 1. The refrigerant is A2L classified, i.e. non-toxic but slightly flammable. Because of this, the heat pump is fully enclosed and equipped with a gas leak sensor and ventilation.
The heat pump is connected with remote connection to the Oilon Global Monitor control system, which monitors equipment performance, usage rate, power generation, and immediately reports any possible abnormal operation.
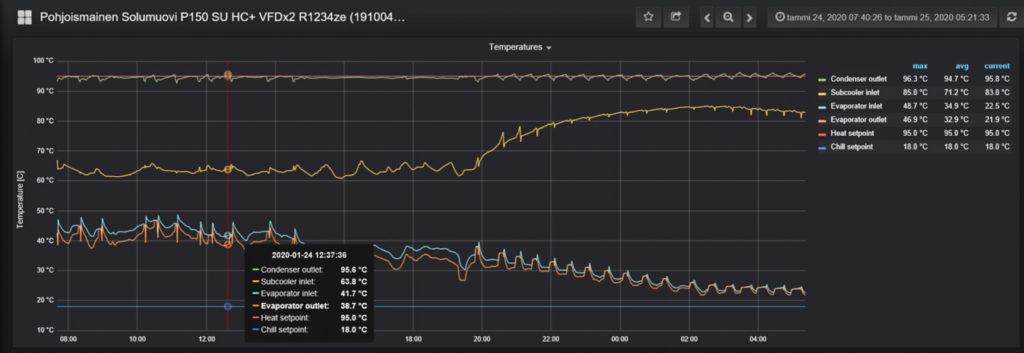
Affordable and functional package
“The heat pump was taken into operation in early 2019 and we now have 11 months of statistics on its operation,” Mälkönen continues in the interview conducted in January 2020. “During this time, the heat pump produced 413MWh of heat and also significantly reduced the carbon footprint of production. Much more could have been produced, but we had no place where to utilize it. The heat treatment furnaces were under-utilized last year, but this year all four will be fully operational. On the other hand the heating of the property was only connected to the system in the spring.”
“Oilon’s strength is that they know how to calculate, so we got an exactly dimensioned solution and, on the other hand, they also take care of the machine maintenance. Alongside this, our own expertise in implementation made it possible to put in the system at a relatively low cost. The heat pump accounted for a bit less than half of the total investment, and we also received investment support for our project. The payback period will be very reasonable.”
“The risks of the project were high when we started to apply this new technology for a new purpose. However, everything has gone as we had hoped and there has been no trouble with the heat pump during the year. Everything has worked perfectly. I am happy.”
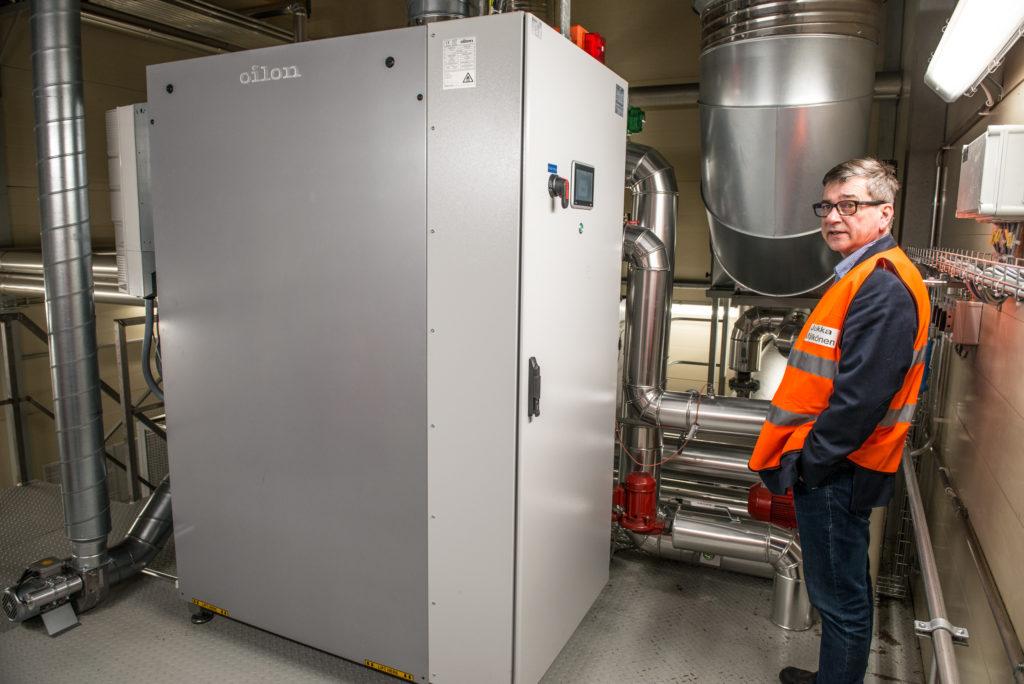