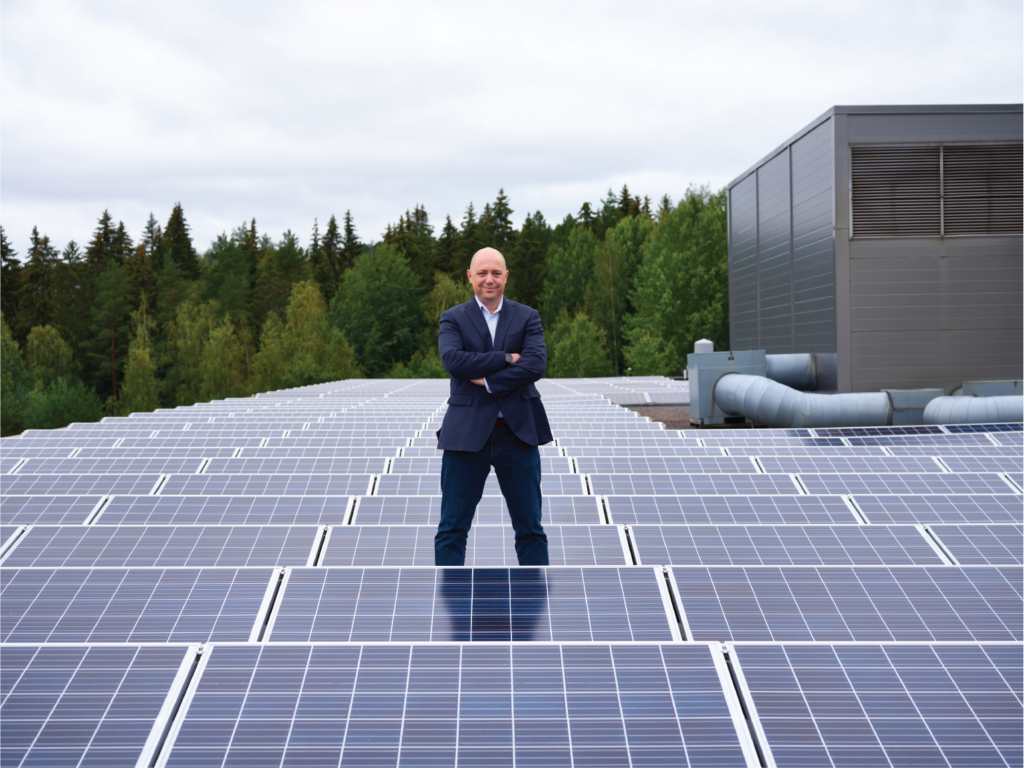
“The climate crisis and the energy revolution challenge both the energy technology sector and companies in general to improve their own business. Oilon stands at the forefront of this change.”
Our climate is changing, and with it, the rules and principles of business. Legislators, investors, and consumers demand companies to go green, and using big words is no longer enough.
In some companies, this transition causes concerns, and in others, it is seen as an opportunity. Then there are the pioneers, such as Oilon, who are willing to stand at the forefront of the change. The company, which celebrated its 60th anniversary in spring 2021, has invested in sustainable development for decades.
“A good example is the nitrogen oxides in burners. We’ve managed to reduce NOx emissions by 80–90 per cent in ten years,” says Oilon’s CEO Tero Tulokas with a hint of pride in his voice. After all, nitrogen oxides are among the most harmful atmospheric emissions from energy production.
This quantum leap in emission reduction was made possible by digital twins. These are exact virtual models that allow Oilon’s experts to improve product performance at a fast pace, as fewer physical prototypes are required for testing. Virtual twins are also used for burner and heat pump monitoring and optimization.
Extending the range of compatible fuels has been another key focus in product development. Currently, Oilon burners can fire practically any of the known biofuels.
“Biogases, bio-oils, ethanol, methanol – we can use any liquid and gaseous fuel available”, Tulokas says. One of the fuels on the list is green hydrogen, which is believed to have huge potential.
One million tonnes of CO2 eliminated
When calculating carbon dioxide emissions for energy production, the biggest factor is fuel choice. However, there is another effective way of improving emission levels: increasing the burners’ adjustment range.
“The smaller the part load at which the burner can operate, the fewer fuel-hungry boiler starts and stops there are,” Tulokas explains. For instance, being able to continue firing at 10% load instead of 25% makes a massive difference. Increasing the burner’s control range can decrease fuel consumption by more than 10 per cent.
Another way to reduce fuel consumption is to reduce residual oxygen content in flue gas, resulting in reduced CO2 emissions. The smaller the residual oxygen content after combustion, the less energy is wasted. Thanks to intensive research and development, Oilon has managed to achieve increasingly lower residual oxygen levels.
In Oilon burners, combustion is managed by an automated system which optimizes the ratio between fuel and oxygen.
The reduction in CO2 emissions experienced by Oilon’s burner customers is often dramatic.
“When an energy company from Beijing switched from coal to natural gas and Oilon burners, the company’s CO2 emissions were reduced by around one million tonnes per year. This corresponds to around 10 per cent of Finland’s transport emissions,” Tulokas says.
Energy companies embrace heat pumps
In international scenarios, heat pumps have been identified as one of the primary solutions for reducing greenhouse gas emissions. For example, the International Energy Agency believes that by 2045, as much as half of the energy required for building heating should be covered by heat pumps. This is due to climate goals – after all, heat pumps are very efficient in utilizing renewable thermal energy from sources such as soil and outdoor air.
“For years now, Oilon has invested heavily in heat pump product development. We can already reach temperatures of 120–130 °C, an interesting proposition especially for industrial customers,” Tulokas says.
One of the focal points in heat pump research is the coefficient of performance, COP. It conveys how efficiently the heat pump transforms electricity into energy.
“When producing heating and cooling at the same time, we can produce up to 10 kilowatts of energy per one kilowatt of electricity,” Tulokas says. In ground source cooling, the COP can be as high as 20–30.
In industrial applications, Oilon heat pumps are typically used for recycling energy. What this means in practice is that waste energy from one machine or process is recovered and reused elsewhere with a good COP.
Oilon has a wide variety of customers around the world. Data centers, wastewater treatment plants, dairies, food processing plants, and chemical industry operators all use Oilon heat pumps.
Companies operating in the energy sector are especially interested in carbon-neutral heat production. One reason for this is emissions trading, which encourages companies to switch away from fossil energy sources. The Finnish energy company Fortum is a good example. The company has procured Oilon heat pumps which will replace coal-based heating in Espoo.
If the entire 11-MW scope of the project is completed, the system will replace around 92 gigawatt hours of coal energy. This corresponds to 31,000 tonnes of CO2 per year or removing 14,500 cars from Finnish roads.
Walking the talk
For several years, Oilon has worked actively towards reducing the company’s own carbon footprint. Ground source heating is used where possible, factory roofs are now peppered with solar panels, and there have been energy system upgrades at Oilon properties.
In the fall of 2021, Oilon joined the Science Based Targets initiative (SBTi), one of the most influential climate initiatives for the private sector. Members commit to reducing emissions from their own operations in line with the Paris Agreement’s goals.
Oilon has pledged that by 2030, the company will reduce both their direct and indirect greenhouse gas emissions by least 46 per cent from the 2019 levels. At the current rate, this goal will be reached ahead of time.
“Nearly 3,000 pioneering companies have joined the initiative. This is an excellent way to promote both internal climate goals and exercise corporate responsibility,” Tulokas says.
Even though environmental responsibility is a key part of Oilon’s business DNA, it is equally important to develop our economical and social responsibility. “A three-legged stool will always be more stable,” Tulokas sums up.