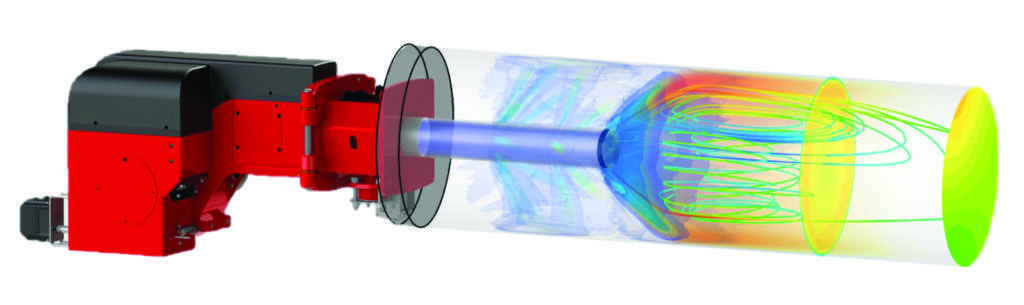
Computational fluid dynamics, CFD in short, is primarily used for numerical modeling of gas and liquid flows. CFD enables Oilon’s experts to simulate different processes, such as a burner’s operation far ahead of creating a physical prototype. This speeds up development, reduces costs, and results in a better product overall.
Nations around the globe are increasingly reducing their NOx emissions. This requires continuous advances in combustion and boiler technology, but there is also another factor to consider: which fuel to use. Oilon has made developing Low-NOx combustion technology a priority. Another focus area are alternative fuels that meet the criteria for sustainable development. In recent years, the company’s efforts have focused especially on low-NOx solutions for natural gas. Let’s take a look at one example.
LN30 Ultra low NOx – a new family of burners
“This is where the magic happens, in the combustion head,” says Joonas Kattelus, Oilon’s chief technology officer. “We have recently introduced a new Monoblock product family, the LN30. When firing natural gas in these burners, we can achieve the record-breaking Ultra Low NOx level, below 2.5 ppm (5 mg/Nm3). These are premix burners with a long, tubular combustion head. The smallest member in the family has a maximum capacity of 900 kW (3.4 MMbtu/h) and the largest, 4.9 MW (18.6 MMBtu/h). These are industrial burners and occupy the lower-to-average capacity position in the Oilon product portfolio.

“There have been other premix burners on the market for years already. However, what we are now offering is considerably better than any previous models. For example, let’s compare our new solution to premix mesh burner technology where the fuel–air mixture is homogenized as much as possible by feeding it into the furnace through a tight mesh. Our LN30 burners have no mesh; instead, we use a long tube with nozzles at one end for feeding the fuel and air into the furnace for combustion.”
Kattelus explains that a mesh-based burner requires extremely clean combustion air, as otherwise impurities would clog up the mesh in the combustion head. In practice, effective filtration is a must, and the filter itself would require frequent cleaning. This technology cannot be used in dusty environments. The burners in the LN30 series have no filter; no filter is required, as there are no small openings prone to clogging.
Low NOx emissions at low residual oxygen levels
“One significant new characteristic of the LN30 series is its reduced residual oxygen (O2) level,” Kattelus continues. “In traditional premix burners, the 9-ppm NOx limit can be achieved only with a 7–8% residual oxygen level. With these burners, we can achieve this with an O2 level as low as 4–6%. At 6–8% O2, we can go as low as 5 ppm. Naturally, our goal was to get the residual oxygen level as low as possible, as this improves efficiency.”
“We were able to fine-tune our premix very close to perfection, resulting in a major boost in performance. The mixing process was developed entirely with CFD. By selecting the right shape for the combustion head and the nozzles, and with proper nozzle placement, we managed to keep the flame extremely compact. The flame fits well even in a smaller furnace.”
Kattelus elaborates that a perfect premix will also reduce the risk of CO formation. Typically, when NOx levels go down, CO levels go up. With a perfect premix, all CO is consumed and the problem is avoided.
Another benefit of a long combustion head is that it promotes internal flue gas recirculation (IFGR) in the front section of the furnace. In this process, inert flue gas is mixed into the fuel–air mixture. This cools down the flame, reducing the formation of thermal NOx compounds and enabling the use of a lower O2 content in the flue gas.
“Traditionally, flue gas mixing has been achieved using external flue gas recirculation (FGR), where flue gas is fed into the furnace from the outside. However, external FGR has limitations that can be problematic for some customers in certain situations.”
According to Kattelus, Oilon has verified its new burner family’s delivery reliability and performance with extensive laboratory testing. The products have also been UL-certified. The burner equipment for the first field case in the United States have been commissioned, and more deliveries are currently underway. Oilon has delivered LN30 products to other markets for some years already, with good results.
Oilon has patents pending for the new technology in Europe and China. The technology is already patented in the USA.
CFD modeling is the key to excellent engineering and development
For nearly 15 years, Oilon has utilized CFD calculation in burner engineering and development. Today, CFD is one of the main development tools used at Oilon. In the early years, CFD calculations took a long time to process and tended to deliver inaccurate results, which meant that the tool was relegated to a supportive role. However, as processing power increased, computational models matured and the company’s knowhow expanded, CFD became more viable, and has now served several years as the company’s primary development tool.
“Today, we develop the combustion technology used in our products largely using CFD simulation. Typically, the values we get are pretty much exactly the same as those we measure from the actual physical prototype,” Kattelus says. “We used to make several prototypes during burner development, and testing each a long time. Now, thanks to CFD, we get better results faster and with fewer costs, even in a landscape rife with increasingly stringent requirements. On one hand, the boiler industry tends to keep furnace dimensions as small as possible to reduce costs, and on the other, legislation aims to reduce emission levels. There is a conflict between these two, as a smaller furnace will increase NOx emissions.”
“Naturally, both boiler performance and the amount of NOx emissions depend on both parts of the sum: the burner and the furnace. Emission levels depend on several parameters, but the main rule is that improving the transmission of heat from the flame to the furnace will always reduce NOx emissions. There are many ways to improve this, such as optimizing furnace dimensions, furnace corrugation, and minimizing the use of refractory. CFD modeling allows us to work with boiler manufacturers to ensure the best possible result.”
Unique CFD know-how and an excellent laboratory
Over the years, Oilon has acquired an extensive experience and a unique know-how in utilizing CFD modeling. This expertise is supported by excellent laboratory facilities in the company’s product development center. These two form a combination that is hard to beat: measurements from the laboratory are used to develop CFD models, which, in turn, are verified and further tested in the laboratory. According to Kattelus, the company has the world’s most advanced natural gas combustion models, especially when it comes to emission modeling.