Snellmanin Lihanjalostus Oy (Snellman Meat Refinement) in Pietarsaari is one of the first companies to use industrial heat pumps for waste heat recovery. Today industrial heat pumps from Oilon produce a remarkable share of heating energy at Snellman’s plant.
Snellman is a pioneer user of heat pumps
More than 10 years ago – before anybody actually even talked about industrial heat pumps – Markus Snellman, technical manager at the Snellman meat processing plant, discovered that a lot of energy was wasted with the hot water used for washing.
Warm water with a heat pump
A contact with Scancool that operated in Kokkola, next to Pietarsaari, and which was later acquired by Oilon, gave a cautiously positive answer to Markus Snellman’s question: “Why not a heat pump?” They decided to start a project and see how it would succeed. This happened in 2007.
At a meat processing plant they use a lot of water, about one thousand cubic meters and mainly hot water, every day. The temperature of the grey water after being used for washing and flowing to Snellman’s own treatment plant is about plus 30 degrees centigrade (+30°C), which gave an excellent starting point for the project.
Heating the water for washing takes about one megawatt (MW) of heating power and the warm water is needed 16 hours a day. The heat pump was designed according to this need for hot water. With the heat pump the temperature of the water was raised to +55°C and the result was a saving of approximately 450,000kg of heating oil per year; a semi-trailer load each month.
As for Scancool they found the project so successful that the company decided to start a completely new line of business as a pioneer in the field. This lead to contact with Oilon which subsequently acquired all shares of Scancool in 2011.
Snellman makes things its own way
“We want to be a little bit different and be open about what we do,” says Markus Snellman. “We have made many decisions even if all of them have not been easy. For instance we don’t use any gene-manipulated meat in our production. If at some time there is a shortage of meat, then we live with that. We don’t buy anything else. One has to be honest. If we are not, everybody will know it in a few minutes. Information spreads so quickly.”
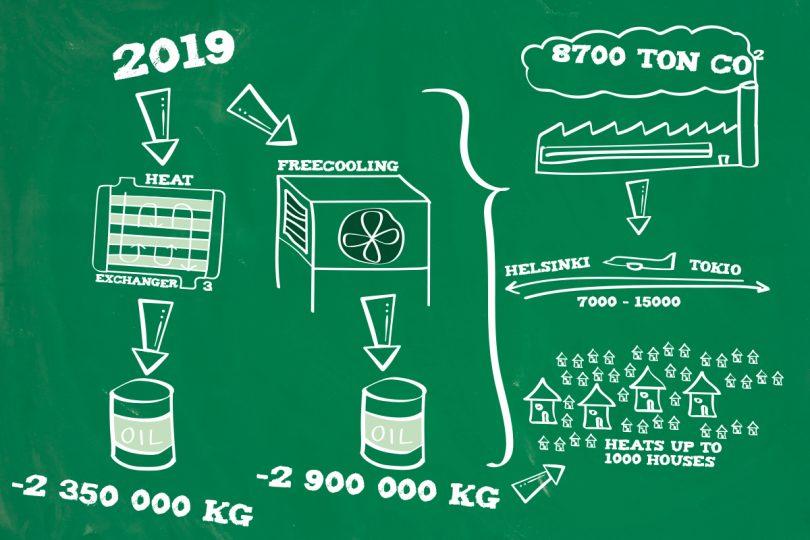
“I love this work! I am responsible for the service and maintenance of the plant and energy is my favourite subject. We have made many renewals during the years and thanks to them our plant in Kuusisaari today consumes 2,900,000kg less oil compared to if we had just twiddled our thumbs and done nothing. It means heating a thousand private houses or 8,700 tons less carbon dioxide – every year.”
“We do much more than what we talk about, but sometimes it is also good to talk. I want to share information and help others do the right things. I have been involved in the projects of our colleague companies Oles Fast Food and Korv-Görans Kebab and both of them have Oilon heat pumps installed. The food industry in the area knows how we have solved things and I have helped them. Also people from our big competitor Atria have visited us.”
“You help the competition?” Snellman laughs at the question. “It is cooperation! The market is huge and global. I want Finland to be strong and this work to be done in Finland. Cooperation is worthwhile!”
More pumps and higher temperatures
The next big step was taken in 2009. There are a huge number of cooling machines at the plant and Snellman realised that the condensing heat was being wasted.
“I asked Scancool if it would be possible to produce 75-degree temperature with a heat pump,” continues Snellman. “‘Yes, it should be okay,’ was the answer. We made small changes, installed heat exchangers before the condensers on the roof and were able to recover much more energy. And we got it every hour, not just during work shifts 16 hours a day like with grey water.”
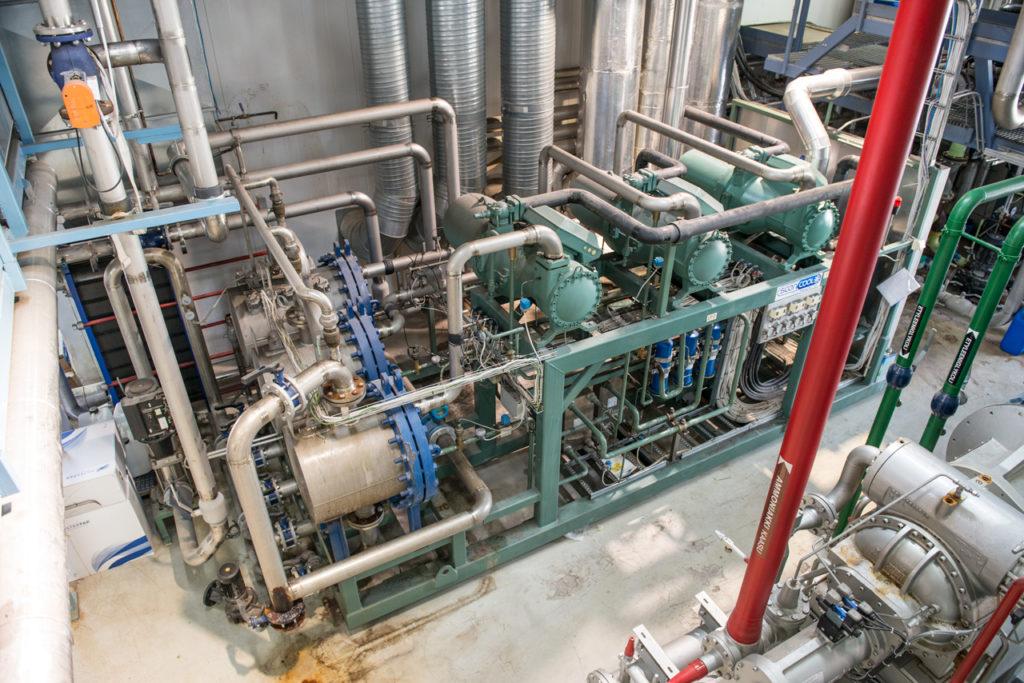
“With this energy we were able to heat the building and the whole process. Butchery, blanching machine and the whole production uses a lot of heat, about +60°C water. Melting cabinets, the whole metwurst factory.”
The latest step is two Oilon ChillHeat industrial heat pump installed in January this year, 2019, producing a temperature of +95°C. It is needed, for example, for sterilising knives and other tools which requires a temperature of at least +82°C. The heat is also used for drying spaces after washing. The refrigerant in the pumps is R1234ze, which has almost zero GWP value.
The high temperature had previously been produced with steam from a biogas boiler. The Snellman meat processing plant moved to using biogas in 2014, replacing an oil-based system. Steam from the biogas boiler is now used much less, mainly for cooking sausages and hams.
Oilon is a good partner for Snellman
“It is easy to work with Oilon,” says Snellman. “When I ask if they can do this or that, the answer is: ‘yes, surely’. When I ask if they can do +95°C, I hear: ‘certainly’. I will soon ask the next question: when do we get +150°C? I believe it is not very far away. Then we will no longer need the steam boiler.”
“When we install a heat pump we save the environment and also money. Last year we saved 580,000€. And we save it every year! Heat pumps produce thermal energy four times the amount compared to consumed energy. Investment in a heat pump pays itself back in almost one year so it is difficult not to buy.”
Markus Snellman, who has been with the company for 25 years, studies and continuously observes technology development. He has clearly mastered energy issues very well.
“Our first heat pump was one of the first industrial heat pump in the foodstuff industry,” says Snellman. “We have a very good cooperation with Oilon and we walk at the forefront of the industry. ‘Energy gurus’ sometimes phone me but the discussion ends very quickly when I tell them what we have done.”
“Our biogas burners are from Oilon. Oilon has a very high competence in energy issues. They rule both automation and energy theory – and they can calculate the best solution.”
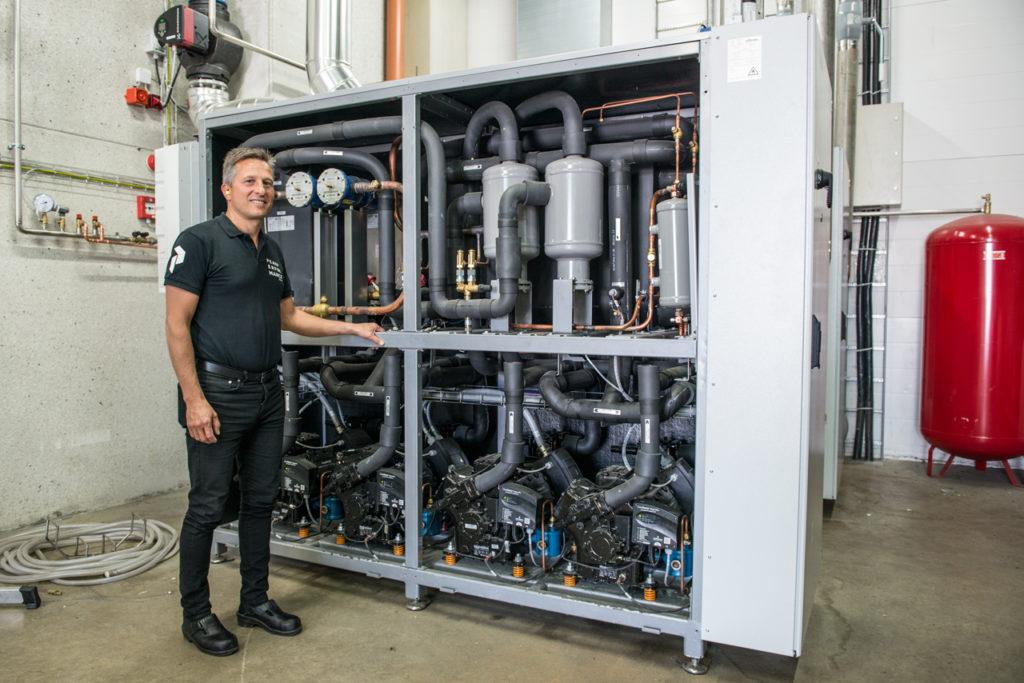