Oilon Oy has developed a family of heat pumps which can be set up for a client’s specific environment through a set of options. The firm is really now offering the mass customisation of heat pumps.
Industry and energy provision need heat pumps. However, temperature levels, energy requirements and other circumstances vary a lot and require equipment adjusted to the situation. At the same time the equipment must be highly efficient, easily controllable and suited for high temperatures. Moreover the heating system designers need tools for easily and quickly selecting the exact solution.
From cooling system contractor to heat pump manufacturer
“Everything started from Scancool Oy, which was a traditional contractor in the cooling business,” says Juha Aaltola, Doctor of energy technology, and product development director of Oilon Oy. “A large customer in the foodstuff industry considered the possibility of utilising waste water heat and the completed project was so successful that a decision was made to start a completely new business area. At that time in 2008 I joined the company to start and manage the heat pump business as a business director.”
“At that time industrial heat pumps didn’t exist but a couple of years later there were plenty of them. We were the pioneers of the business. Sitra (the Finnish Innovation Fund) and the venture capital investor Wedeco Oy were already involved in the business and then in 2011 Oilon acquired the whole company. The rest is now history.”
Refrigerants are a compromise of many properties
In a heat pump a compressor pumps gaseous refrigerant into a condenser where it condensates to liquid and releases thermal energy. From the condenser the liquid moves via an expansion valve to an evaporator, evaporates to gas, recovers energy and continues its way to the compressor.
By utilising the phase change it is possible to move quite large amounts of energy with a relatively small mass flow of the refrigerant. The circulation between condenser and evaporator is continuous and the basics of the technology familiar to all professionals in the area.
“Thermodynamic properties of refrigerants are highly variable,” says Aaltola. “With a good refrigerant one can produce a lot of cold and heat with a small mass and volume flow and in a way that relatively little power is needed in the compressor.”
“The reverse side is that such substances may cause ozone deployment or climate change. Some substances are flammable and others poisonous. Since the 1930s, CFCs, such as Freon, started to become common. The ODP effect (Ozone Deployment Potential) was, however, very high and use of those substances started to be restricted from the end of the 1980s. After that HFC substances became common. Their ODP value was zero but GWP value (Global Warming Potential) very high. An alternative has always been natural refrigerants that have limitations because of a.o. toxicity, flammability or requirements of high pressure.”
During the last few years one of the most important focuses of product development at Oilon has been new environmentally friendly refrigerants and the technology connected with them. One of the new refrigerants used by Oilon is, for instance, R1234ze, which is non-toxic, it doesn’t harm the ozone layer and the GWP value is one.
Many new refrigerants also have a low condensing pressure, and by using the right technology it is possible to produce higher temperatures than previously. According to Aaltola, since last year Oilon has achieved a temperature level of 140 degrees centigrade (°C) while 100°C is commonplace.
High efficiency requires the right design
“In many industrial heat pumps on the market the starting point has not been a heat pump but, for instance, cooling water,” continues Aaltola. “With us the starting point of design and everything we do is always heating and as high quality and versatile a heat pump as possible.”
“In cooling devices the pressure difference between the warm and cold side is typically lower and also in other ways the targets of design are different to a heat pump.”
“The efficiency of a heat pump, COP (Coefficient Of Performance) is highly dependent on the temperature difference it produces,” explains Aaltola. “Less electric power is needed when temperature difference is smaller. We utilise this characteristic in many cases by connecting two or more pumps in series, so each unit produces a much smaller temperature difference. This kind of implementations, however, requires versatile products, advanced automation and at the design stage a highly developed selection tool such as the Oilon Selection Tool.”
“At the beginning we used spread sheets of our own for designing heat pump machinery and complete systems but they were difficult to use. Then we started building a Java-based comprehensive program that takes into consideration everything that is needed. I can claim that we are the first firm which has developed a user-friendly calculation program for dimensioning industrial heat pump systems in this scale. With the Oilon Selection Tool it is possible to choose many innovative technologies that improve COP or other characteristics, such as series connection, subcooling, economiser, various refrigerants, inverter power control, partial load simulations etc.”
Reliability requires a tested entirety
Industrial heat pumps are a strongly developing business. Oilon has developed its business into a mass customised series production, where tested basic equipment is furnished with tested options and the result is a completely tested system that fulfils the exact needs of the customer.
“Ten years ago we designed the systems, manufactured the pumps and installed the system at the customer’s place,” says Aaltola. “Now we concentrate on manufacturing excellent equipment and delivery with comprehensive connection instructions.”
“A large number of competitors sell heat pumps that are designed to operate only under certain conditions. However, the operating conditions of industrial heat pumps are often very variable. Depending on the conditions and implementation, the same device may produce, for example, a power of 100 kilowatts (kW) or 600 kW. It is not possible to replace for instance the heat exchanger in such heat pumps with a more suitable one, so the operation under different conditions is not optimal.”
“On the other hand, many of our competitors design their heat pumps individually for each location, so the result is always a new kind of individual, a prototype in a way, that has not been tested in advance. Controllability, operating area and optimal efficiency are results of meticulous testing. If the devices are not tested standard products, there is a high risk that something in the complete system doesn’t meet expectations.”
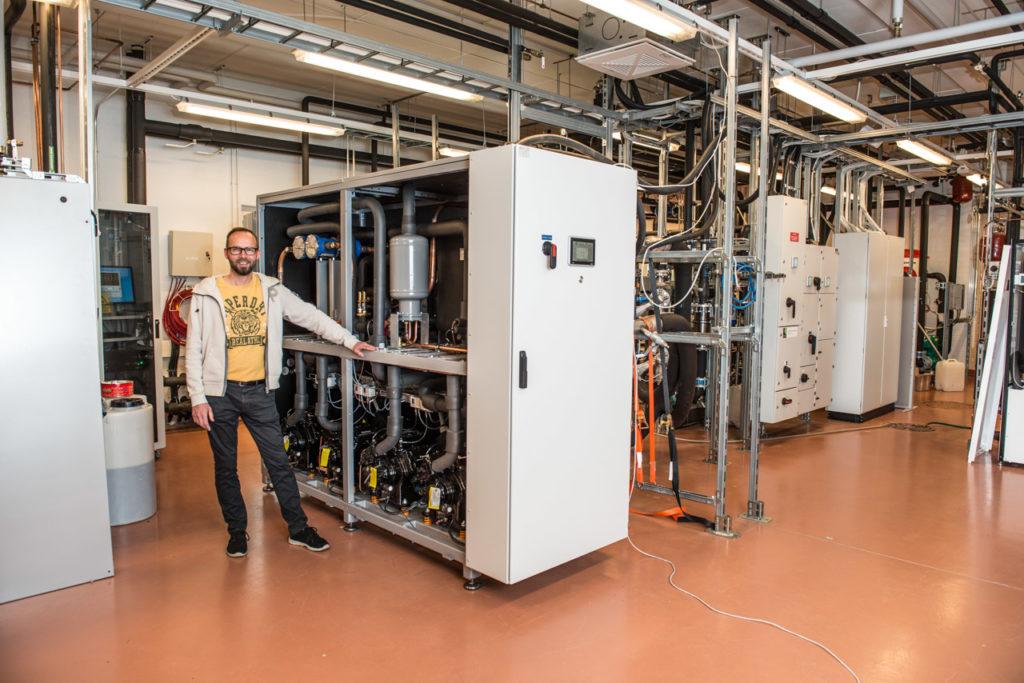
All alternatives in a PDM system
According to Aaltola the starting point at Oilon is always a certain standard product and the operation of the product is adjusted through the choice of refrigerant, condenser, subcooling, economiser and vaporiser together with control options. The final result consists of tested sub solutions and the complete system operates the best possible way in the circumstances it is designed for.
Comprehensive product data management is elementary for effective and economical manufacturing. Oilon’s PDM system (Product Data Management) includes all alternatives and options. A 3D model of the product is also made in the system for preparation to manufacture.
Manufacturing takes place according to ‘Lean’ principles and each device goes through eight manufacturing stages. The manufacturing process is what creates the quality and the whole workflow is developed with an aim for high quality. Each stage includes certain inspections and the device is not moved to the next stage until the inspections are made and documented. In the final test each heat pump is tested in circumstances that are equal to the customer’s operating environment.
Global monitoring and IoT lead the development
Most of the heat pumps from Oilon are connected in a data network and send data of their operation to the cloud. The system very quickly gives information if there is a problem in the operation of the equipment. The system has been in operation for five years and it is continuously being developed further.
It is often possible to remote service the devices thanks to a wealth of historical information. According to Aaltola it is possible for the technician to estimate with the information from the system what tools and spare parts will be needed for a service visit – and if any visit is needed at all.
The customers can have reports that detail the system’s utilisation rate, energy production and money savings. Artificial intelligence under continuous development identifies the performance of the equipment and helps its optimisation, while data mining based on big data helps to anticipate eventual problems.
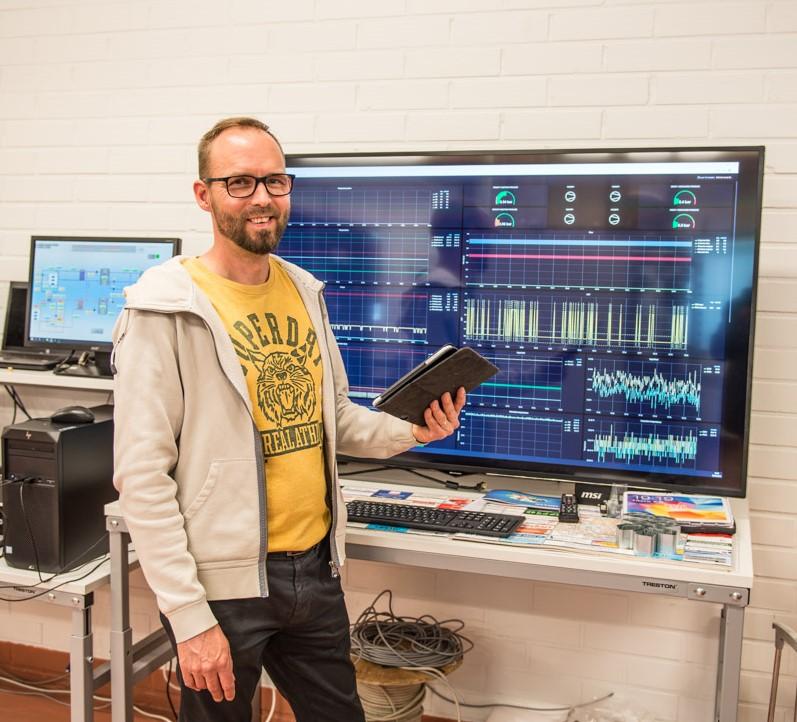
Innovative and open-minded development
“The development of an expansion valve is just one small example of the results of our progress,” says Aaltola. “It is an intelligent device based on anticipating adjusting and includes both a physical device and a program algorithm. It is a good example of how competent and open-minded our R&D people are. Not many – but extremely good people. Our high-performance development is based on them.”