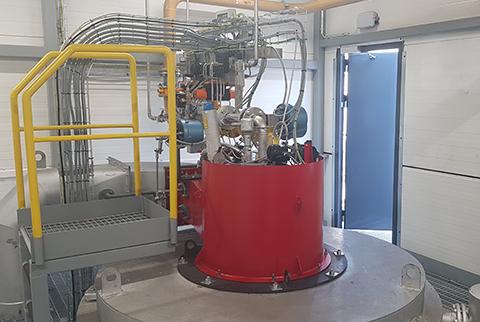
To combat climate change, we need new ways of producing energy. Hydrogen has attracted perhaps the most widespread interest as a potential replacement for fossil fuels. Oilon’s experience in hydrogen combustion spans more than three decades.
Hydrogen may be the most abundant element in the universe, but on Earth, it doesn’t exist on its own freely. There are many ways to produce hydrogen. It can be derived from fossil fuels or produced through electrolysis: by splitting water molecules with electricity. Additionally, hydrogen is produced as a by-product of chemical processes. More than 95% of the hydrogen currently produced is derived from fossil fuels, and the rest from water with electricity through electrolysis. Producing hydrogen through electrolysis has an efficiency of around 60–70%. If the converted hydrogen needs to be transformed back to electricity e.g. through combustion, the round-trip efficiency of the process is only around 30%. Consequently, hydrogen is not an efficient alternative for using electricity directly.
Due to its environmentally friendly nature, hydrogen produced with renewable electricity is referred to as green hydrogen. The amount of green hydrogen we will need in the future is enormous. To illustrate, the amount of renewable electricity required to produce enough green hydrogen to cover the current production of fossil hydrogen alone surpasses EU’s annual electricity consumption. This would mean 4,000 TWh or around 160,000 new major 6 MW wind farms. A good starting point, to be sure.
In the fight against climate change, we need to use all the tools at our disposal. Everywhere around the world, there are major initiatives on large-scale green hydrogen production. The European Commission estimates that in the next three decades, European governments will invest a total of EUR 470 billion into renewable hydrogen.
In the green transition, hydrogen is seen to have great potential as a form of energy storage that would even out production spikes in renewable energy production. In practical terms, this would mean producing hydrogen with surplus electricity generated by decentralized solar plants and wind farms. This hydrogen would act as storage for the energy produced.
Hydrogen combustion – special considerations and applications
“Oilon has more than 30 years of experience in firing fuels that contain hydrogen. We offer several hydrogen-compatible burner models,” says Oilon’s Chief Technology Officer Joonas Kattelus.
Oilon’s entire range of burners for gaseous fuels is well suited for firing mixtures with up to 20% hydrogen content without modification. If hydrogen content is increased to 20–70 per cent, a nozzle structure specifically designed for the purpose must be used. At higher levels (70–100%) and when there is variation in the fuel’s hydrogen content, a comprehensive solution designed for hydrogen combustion is usually required.
Compared to natural gas, 100% hydrogen has a lower density and energy content per unit of volume. Pure hydrogen is extremely flammable, and it burns very intensely with a hot flame. Hydrogen needs to be fed into the flame zone in a way that prevents damage to the burner’s nozzles and structures. It is also important that the fuel stream and its flow rate is appropriately aligned and controlled. There are some other limitations, such as that premix burner solutions are unsuitable for firing 100% hydrogen. As hydrogen is extremely flammable, safety is an absolute priority. All gas pipes must be equipped for purging the lines with non-combustible gas. The most common solution is to use nitrogen to flush hydrogen out of the pipes when the burner is switched off.
Hydrogen as a fuel
“Oilon has designed and delivered hundreds of burners for different hydrogen mixtures across the globe. Hydrogen content varies from a few per cent all the way to 100 per cent. Over the years, we have accumulated extensive expertise in the field. Thanks to this, we are well equipped to utilize hydrogen in burner combustion,” Kattelus says.
A typical use case for hydrogen combustion is the metal industry with its extremely high production temperatures. Another sector that uses hydrogen as an energy source is the chemical industry, where hydrogen is produced as a byproduct. For oil refineries, Oilon has delivered several projects where the fuel used is refinery gas. The chemical composition of refinery gases tends to vary greatly, which means there are large fluctuations in hydrogen content.
In steel production, coke oven gas (COG) generated as part of the process and blast furnace gas (BFG) are commonly used as a source of energy. COG has a high hydrogen content, while BFG’s hydrogen content is lower. Some of the COG and BFG projects Oilon has completed have involved extremely strict emission requirements. Additionally, Oilon has extensive experience in town gas combustion. Depending on the production process, the hydrogen content of the fuel can vary greatly, the highest levels being 70 per cent.