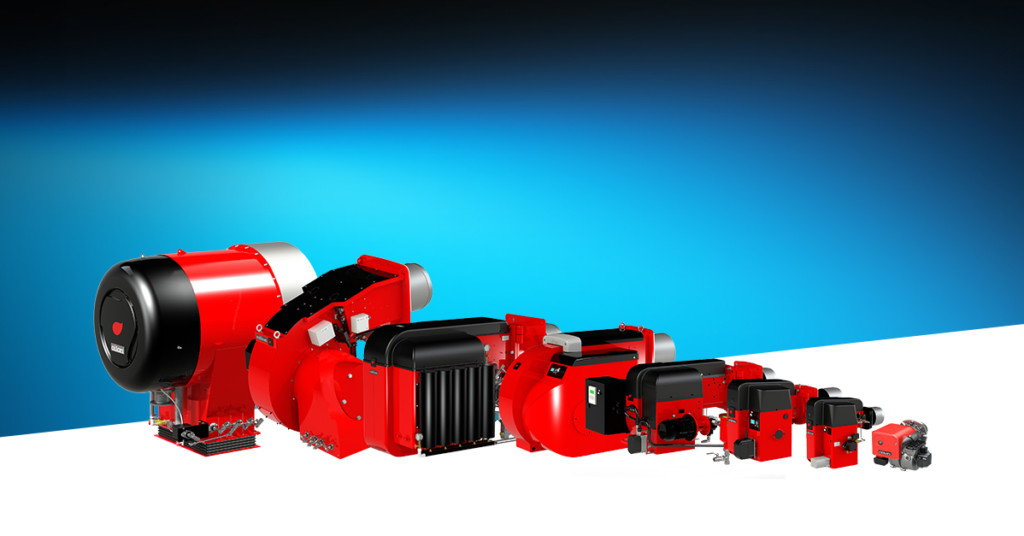
Oilon organized an internal investigation into the sustainability of the company’s burner products. The primary starting point was the EU taxonomy, which sets requirements for investments that support sustainable development. The results were impressive: as many as 92 per cent of the company’s burner products met the criteria.
One of Oilon’s primary goals is to be a leading manufacturer of clean combustion technology. The company allocates more than 6 per cent of their turnover to product development. In recent years, Oilon has invested heavily in heat pump technology. However, clean combustion products continue to play a critical role in Oilon’s business.
“In the future, a substantial portion of combustion will be replaced by electricity-based technology, such as heat pumps and electric boilers. This is especially true in low-temperature applications,” says Oilon Group’s Chief Technology Officer Joonas Kattelus. There are still many applications where combustion is necessary. In ships and planes, for example, fuels are an excellent way to store energy. They can also be used to balance out the supply and demand for heating. In such applications, replacing fuels exclusively with batteries is not sensible. Correspondingly, process and industrial applications will continue to require the high output temperatures provided by combustion technology far into the future.
Fuel is the single largest factor
As a rule, gaseous fossil fuels generate lower emissions than liquid fossil fuels. When fired, fuel oils release not only CO2 but also sulfur dioxide, nitrogen oxides, and various particulate emissions, such a soot. Compared to oil, natural gas burns extremely cleanly. It has zero sulfur dioxide and soot emissions.
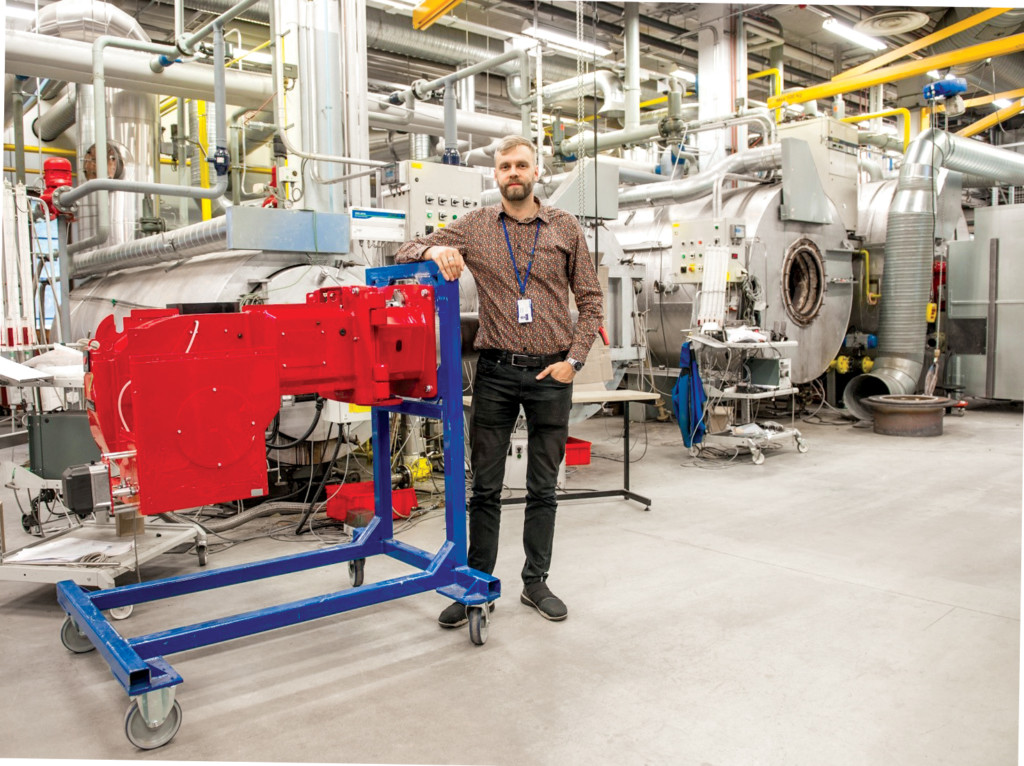
According to Kattelus, the majority of the company’s portfolio was recognized as sustainable. This included all products that fire sustainable fuels, traditional and low-NOx natural gas burners, as well as start-up and support burners delivered to waste incineration facilities and plants that utilize biofuels.
“This breakdown was based on the idea that if we replace coal combustion with natural gas in China, for example, we achieve a massive one-off reduction in NOx, particle, and CO emissions.” Kattelus estimates that coal combustion generates roughly twice as much CO2 as firing natural gas.
Like any fossil fuel, natural gas combustion does produce CO2 emissions, which increases and intensifies the greenhouse effect. According to Kattelus, Oilon has managed to reduce the other emissions to such as low level that combustion itself is extremely clean.
Russia’s war of aggression against Ukraine has dramatically change the global energy landscape. This shift speaks for phasing out natural gas as an energy source. The idea is further supported by the fact that renewable fuels typically have smaller CO2 emissions than fossil fuels.
“Currently, governments around the world are especially interested in hydrogen. Hydrogen can be produced through electrolysis with sustainable electricity, such as wind power. In this application, it serves as a form of energy storage,” Kattelus says.
From the combustion standpoint, hydrogen is clean, as its combustion product is water. However, hydrogen burns very intensely and with a hot flame. The hotter the flame, the more harmful nitrogen oxides, or NOx compounds, are formed. In Oilon ACE burners, NOx emissions are minimized with combustion air and fuel staging, which results in a wide, cool flame. Additionally, the flue gases generated during combustion are directed back into the flame inside the boiler, further cooling down the flame.
Hydrogen is not a foolproof solution. Current infrastructure is unsuitable for hydrogen storage and transportation without extensive retrofits, and hydrogen requires additional attention to safety. One alternative to clean hydrogen is synthetic methane made from hydrogen. Methane has almost exactly the same properties as natural gas, which allows it to be used directly in current systems. Hydrogen can also be used to produce ammonia, which is completely free of CO2 emissions. Ammonia is not without its problems: it is toxic and has high NOx emissions.
“Operators in Far East seem to be especially interest in ammonia. In Japan a South Korea, people are investigating new solutions,” Kattelus says. In large coal plants, ammonia is seen as a fuel of the future, and many boiler manufacturers have already asked if their boilers could be converted to ammonia use.
Adopting renewable fuels requires investments. According to Tapio Murtonen, Oilon’s Chief Business Officer , if you want to use another fuel in an Oilon industrial burner, a new burner is typically required. In process and power plant burners, a less extensive retrofit is required.
“In a typical retrofit project, we will install the necessary fuel lances and valve units and make some adjustments to the automation,” Murtonen describes.
Achieving circular economy and protecting the environment
In industrial operations, a large portion of the side steams still goes to waste. It used to be commonplace to get rid of challenging process-based fuels through flaring. This is no longer always the case, as the interest in alternative fuels and utilizing waste energy has increased due to increasingly stringent emission standards and rising energy prices.
“Initially, gases would be released to the atmosphere, then flaring was invented. The energy was lost in the winds, but the emission levels dropped. In modern solutions, the gases are fired in a boiler, allowing companies to recover the energy contained in the gas,” Murtonen says.
The more process industry side streams are harnessed, the more the range of available fuels will increase. Already today, Oilon delivers burners for various challenging fuels, such as the blast furnace gas and coke oven gas generated by steel production. Additionally, the company has decades of experience in oil refinery and process industry gases.
“The fuels produced as a byproduct are not always uniform, and the inlet pressure can fluctuate. We need to design the equipment so that variance is under control. This requires different sensors, regulators, and special automation solutions,” Kattelus says.
According to Kattelus, pyrolysis oils have recently started to generate renewed interest. After the early 2000s, they were dismissed as too challenging to be used as a fuel. Being acidic, pyrolysis oils would corrode components, and their properties could suddenly change, clogging fuel lines. There is some indication that the latest pyrolysis oils have better properties. The PH value is still low, which means that the components must be made of acid-proof steel.
Oilon burners are also used in fluidized bed boilers as start-up and support burners. These boilers are used for firing biofuels and for producing energy from municipal waste left over after recycling and reuse.
“Fluidized bed boilers, which are most often used to fire woodchips and similar biofuels, were recognized as sustainable. The boiler is first heated up to 850 °C with start-up and support burners, after which biomass or municipal waste is fed into the boiler,” Murtonen says.
For many types of hazardous waste, incineration is the only reasonable disposal option. In hazardous waste management facilities, gases and liquids are fired with special burners. Part of the waste is fed past the burners into the boiler, where it is incinerated safely. This way the hazardous waste can be prevented from harming the atmosphere, waterways, and terrain.
The last eight per cent – a problem or an opportunity?
Oilon still produces burners that do not meet the criteria for sustainable development. The last 8 per cent of the portfolio consists of heavy oil burners and light fuel oil burners, which are primarily used by the marine industry.
“Burners that use only oil as a fuel account for a relatively small portion. For the most part, the products are gas and gas/light fuel oil burners,” Murtonen says. In the long run, Murtonen believes that the share of oil burners will decrease even further, as marine regulation becomes more stringent every year. When discussing future fuels in the marine industry, three candidates rise above the others: ammonia, synthetic methane, and synthetic methanol.
“The marine industry is looking for new solutions. We have some methanol projects underway as well. We have started discussions with classification societies, exploring what kind of equipment and safety systems will be required. Additionally, we’ve started development initiatives with some of our customers,” Murtonen says.
“Methanol is an option that seems to pop up frequently,” Kattelus confirms. “It is a good renewable fuel: a liquid fuel that doesn’t need to be pressurized, which simplifies logistics. In many respects, methanol is similar to light fuel oil, which means that our current technology can be used with relatively minor modifications.”
Methanol is a forest industry side stream and a byproduct of biodiesel production. It can be produced from biomass, hydrogen, and fossil sources. Regardless of the source, methanol has substantially lower emissions than traditional fossil fuels.
In land-based applications, biodiesels have proven to be an excellent alternative to traditional fuel oils. According to Kattelus, the properties of the Finnish Neste My biodiesel are so close to traditional fuel oil that it can be used with current technology and, at the same time, reduce the plant’s emission levels. In Oilon burners, you typically only need to replace the flame detector to make the entire burner range compatible with biodiesel.
The best burners in the world are made for real-world conditions
Oilon uses computational fluid dynamics (CFD modeling) as part of the product development process. The company’s experts create digital prototypes and simulate burner operation before building a physical prototype.
Increasingly stringent emission ceilings require extremely careful engineering and extensive testing. With CFD modeling, Oilon can simulate dozens or even hundreds of different burner geometries before creating the first prototype.
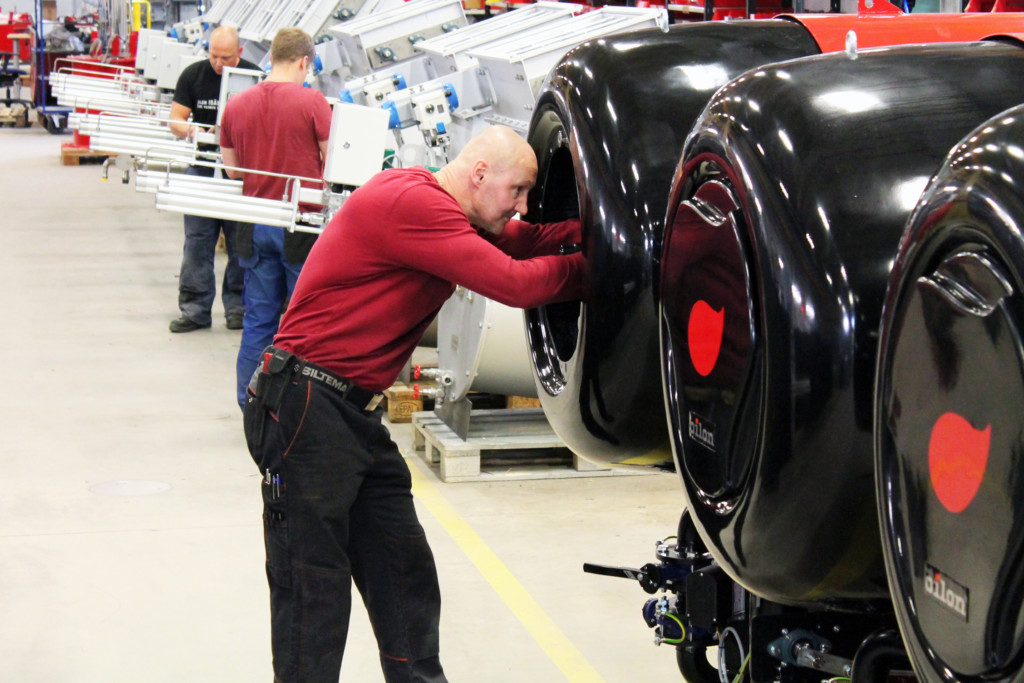
Antti Hämäläinen works as a product developer at Oilon. One of his main jobs is to test Oilon ACE burner products.
“We make countless changes to the prototype. It’s not often that the burner is completely ready after CFD,” Hämäläinen says. “When we test our products, the goal is to get the conditions as close to those at the customer’s plant. We have a lot of different boilers, and we always select the one that is closest to the customer’s boiler.”
The product developers draw fuel lines to the burner and build the required automation. Air temperature, humidity, and pressure all influence the combustion process. There are numerous other factors, some of which can be impossible to take into account. This makes feedback from the field worth its weight in gold.
“The situation at the customer site can change rapidly,” Hämäläinen says. “Here at Oilon we can do almost anything, but the personnel on the field do not have a toolbox that would allow them to fiddle with the tiniest details. This is why we test different settings in several furnaces, making sure that the product is ready. The goal is that you can simply bolt the unit to the boiler and press start. If there are problems, we will recreate the conditions as closely as possibly at the lab and troubleshoot the problem through testing.”
Installation sites and customer needs vary greatly, and there have been some surprises over the decades. Mechanical Engineer Jarmo Haverinen reminisces about problems caused by unusual transportation arrangements. In one case, burners were attached to boilers already at the customer’s factory. The burner–boiler combinations were taken to the installation site by truck, and some burners became damaged during transit. Once the issue was identified, the customer could be advised on how to support the burners, avoiding damage to burner flanges.
Ignition problems are another topic about which Oilon collects data from the field. Practical experiences have shown that careful testing is essential. When the production of a certain ignition transformer ended, the company had to find a replacement as quickly as possible. At the customer site, it became apparent that the new component had a lower ignition current, which caused problems with long ignition cables. The issue was corrected and Oilon learned a valuable lesson.
“We perform so much testing at the lab that the machine is fully operational and ready for use. We perform tests upon tests and run the machine in all possible combinations. The final product looks completely different from what we started off with. That’s what product development is all about,” Hämäläinen concludes.
Standardized products ensure availability
Murtonen agrees that it is essential to make sure the products are ready for use. Even though performance and emission levels are a priority, reliability is what serves as the foundation.
“The burners must be reliable, which means that they need to be robust and ready to use at all times. In a word, the burners need to have an excellent availability,” Murtonen says. Another significant factor is the burner capacity range. Steam boilers, for instance, require a wide turndown ratio.
Installation sites and applications vary greatly. Burners used in marine environments and those using corrosive fuels need to be corrosion-proof. Luckily, customers can anticipate their future needs – an important consideration, says Murtonen, as a burner will serve the customer for around 25 years.
The decrease in natural gas availability in Europe generated strong demand for dual-fuel burners and other alternative burner solutions. Increasingly often, customers select a product with minimal emissions, and oil is no longer viewed as a sustainable solution.
“What sets us apart from the competition is that we achieve the lowest emissions in the world with good efficiency and low residual oxygen,” Murtonen says.
For example, Ultra Low NOx burners based on pre-mix technology can achieve emission levels lower than 2.5 ppm (5 mg/Nm3). Even with their top-tier performance, the burners are easy to maintain and install. The bulk of the technology is the same as in traditional burners.
Adapting clean combustion technology to varying conditions requires balancing out countless factors. However, since the products are standardized, planning out a system takes little time, and stable performance is guaranteed. According to Murtonen, the customer simply indicates the emission requirements, and a suitable burner is selected based on this information. If the customer needs an Ultra Low NOx burner, for instance, there will be no additional work involved.
“Power plants may require solutions with multiple burners. In these projects, we need to consider burner placement, meaning how the burners should be located on the boiler walls for optimal emission performance,” Murtonen describes. “Oilon’s team of experts will handle this and find a solution by selecting the burners and the necessary automation. Once this is completed, the delivery proceeds as usual.”
Oilon’s product selection promotes circular economy. The company’s burners can be used to produce clean energy and harness side streams. Oilon industrial heat pumps, in turn, allow operators to use the produced heat more efficiently and utilize energy that would otherwise be evaporated into the atmosphere.
In the future, more electricity-based sources will be used, decreasing the share of combustion technology. At the same time, in light of ever-tighter emission standards and the expanding range of clean fuels available, there will be a need for increasingly versatile combustion solutions. Sustainable burner solutions and systems based on renewable energy complement and support each other.
Learn more about Oilon burners here Burners – Oilon
Contact us Contacts – Oilon